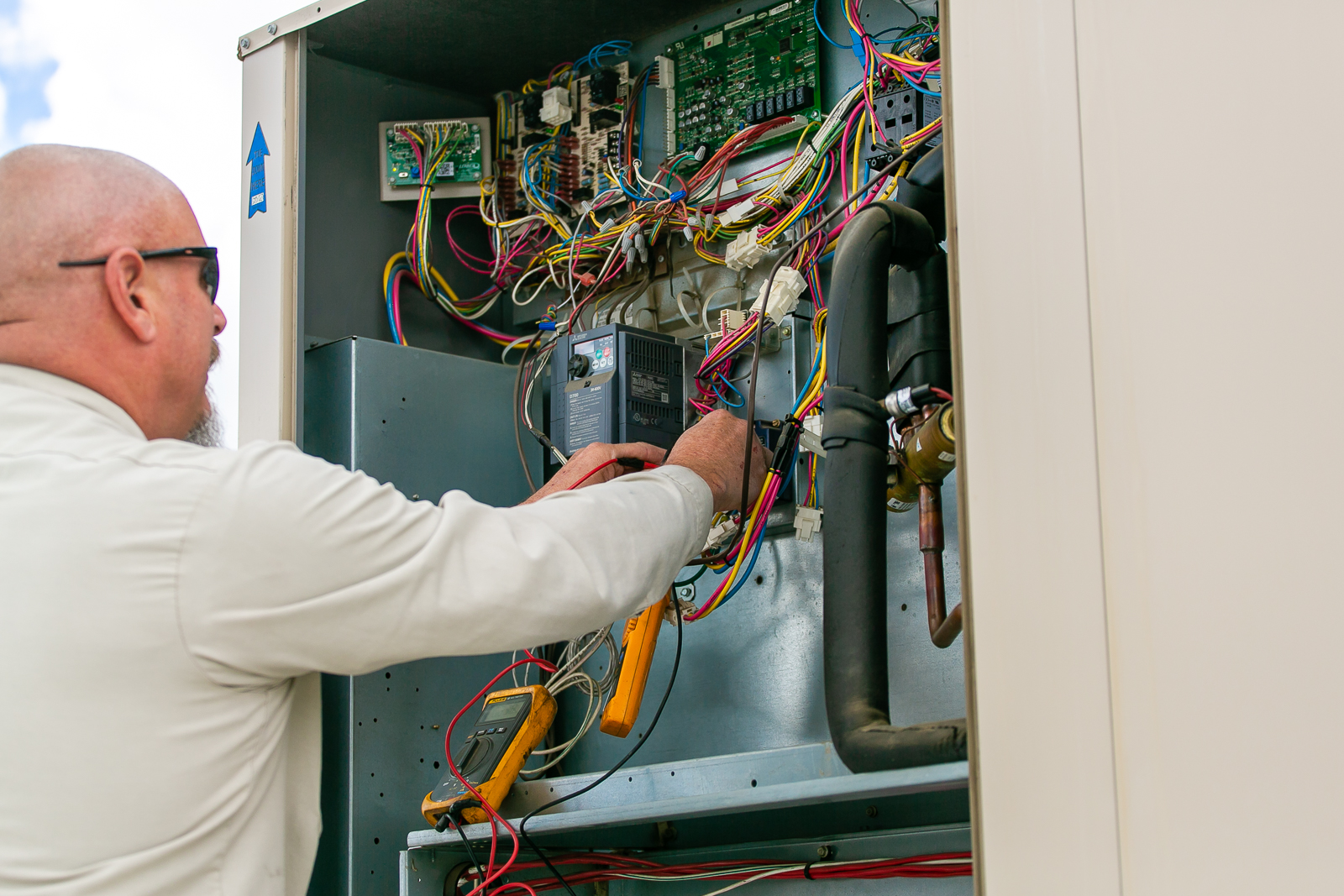
How to Evaluate your Preventive Maintenance Program Before the New Year
As we head into 2021, business owners and managers are looking inward. The end of year is a prime opportunity to plan investments and evaluate current preventive maintenance programs and strategies. But when evaluating these programs, what exactly should you be scrutinizing and how do you know whether or not to make changes?
Let’s take a look at what constitutes a preventive maintenance program and identify what questions you should be asking yourself as you close out the year.
What Is Preventive Maintenance?
Many organizations tend to use preventive maintenance as a “catch-all” phrase; however, the ultimate goal of preventive building maintenance is to achieve operational efficiency.
“Operational Efficiency represents the life-cycle, cost-effective mix of preventive, predictive, and reliability-centered maintenance technologies, coupled with equipment calibration, tracking, and computerized maintenance management capabilities all targeting reliability, safety, occupant comfort, and system efficiency.” —O&M Best Practices Guide
As you can imagine, all preventive maintenance programs are unique (or, at least, they should be unique). Each organization has different needs and goals, which is then coupled with their unique set of tools, equipment, and solutions. While there are standards for preventive maintenance, these standards should merely be used as a foundation with which to launch your own preventative maintenance program.
Although preventive maintenance will look different to everyone, the following is a list of general questions you should be seeking answers for when selecting a service partner for your preventive maintenance needs:
- How often is service provided?
- What preventive maintenance tasks are provided?
- What coverage/protection/warranty is provided for equipment components?
- What tests are conducted and how often?
- When are inspections completed and how often?
- What services are not included (ex. cleaning, replacement, lubricating, etc.)?
The answers to these questions should hopefully lead you to a relationship with a service provider that is mutually beneficial. in other words, you don’t want to end up with a service provider who is rewarded when your systems fail or components break. You’re looking for a relationship that keeps your systems at optimal performance and saves you from hidden costs associated with services “not covered” in your preventive maintenance program.
What Are the Benefits of Preventive Maintenance?
The benefits of strategic and customized preventive maintenance are far-reaching. They can have a positive and lasting impact on your organization, and here’s why:
- You can save energy: With a comprehensive preventive maintenance solution that provides basic and routine tasks such as coil cleaning and air filter replacement, you can reduce energy waste by up to 25%.
- You can extend the life or your equipment: Equipment replacement can be costly to an organization, but with preventive maintenance, you can add up to 10 years to your system and lower the annual cost of equipment replacement by up to 40%.
- You can reduce downtime: When you keep your system functioning at optimal performance for extended periods of time, you can maintain critical processes, minimize downtime, and improve productivity, revenue, and reliability.
- You can improve comfortability: A customized preventive maintenance program can also be customized to enhance the experience of your guests and employees. Simply speaking, this customization can improve indoor air quality and create a safer, cleaner, and more comfortable indoor environment. Ultimately, this can lead to improved morale and retention.
- You can stabilize your budget: When you reduce your need for unexpected equipment repairs and replacement and reduce energy waste, what you’re really doing is stabilizing your budget. You no longer have to worry about hidden or unexpected costs, and you can now effectively budget for building maintenance.
- You can lower costs: Not only can you budget better with a preventive maintenance program, but you can save better, too. Reduce your annual spend on repairs, replacement, and energy, and redirect those funds to other areas of your business.
Even with all the benefits of preventive maintenance, many organizations are still tempted to either lower or completely eliminate preventive maintenance spend from their budget. However, this would be a mistake, especially during the COVID-19 pandemic. More than ever, it’s important to have a system that stays fully functional and protects your employees and guests from harmful particles. The only way to do this is with a designated partner and program for preventive maintenance in place.
Related Content: 3 HVAC Technologies That Can Reduce The Spread Of COVID-19
Questions to Ask When Evaluating Your Preventive Maintenance Program
What Systems Are Protected? What Systems Aren’t Protected?
When evaluating current or potential preventive maintenance programs, it’s critical to determine which areas are and are not protected or provided for by your service contractor. For example, the HVAC unit itself is obvious — but what about server rooms, building controls, and air distribution systems below the roofline? To have a preventive maintenance program that truly provides all the intended benefits, all connected systems and programs must be provided for. Have your contractor outline all areas covered by the preventive maintenance program.
What Is the Service Interval?
For a preventive maintenance program to be beneficial for your company, preventive maintenance actually needs to be provided. While it may seem obvious, it’s a rather simple matter to overlook during contract review. How often are preventive maintenance services provided and what is the rationale behind it? Are you receiving any preventive services that are customized to your system or do they seem to be generic services that everyone receives? It’s important to review frequency and needs relevant to your business. For example, due to smoke and ash in California, air filters will likely need to be replaced more often. Is this something your provider considers? It’s simple things like these that are often overlooked, and unfortunately, this can have a drastic impact on your system.
How Much Are You Spending?
Reducing cost and stabilizing your budget are both core benefits of a preventive maintenance program. But just because you’re on a preventive maintenance contract, doesn’t mean you should switch to autopilot. It’s important to keep track of your annual spending and to confirm that you’re not spending too much on service calls and repairs. As a rule of thumb, if you’re spending twice as much on service calls and repairs as you are on maintenance, then your program is deficient, and it should be reworked as soon as possible.
How Is the Conflict of Interest Removed?
We mentioned earlier that you don’t want to be partnered with a service provider who is continuously rewarded monetarily when components fail or require service. If it’s not obvious how this conflict of risk is mitigated, then you might need to scrutinize this area the most when evaluating your service contract. How is your service provider guaranteeing quality of service and what is the incentive for them to do so? Typically, service providers offer preventive maintenance at a recurring monthly cost. They want your system to remain efficient and they want to eliminate potential issues before they become problems. By doing so, they can minimize service calls and reduce the time spent working on your system. It’s a win-win for both parties. But for this to be truly beneficial for you, you need to understand where their services begin and end and what exactly constitutes problems and services outside your service contract.
What Is the Quality of Service You Are Receiving?
To help you analyze any services you’re currently receiving or services you’re considering receiving, here are a few questions you should answer:
- Consistent Technician: Do you receive assistance from the same technician(s) every month or do you receive assistance from a different person every time? Oftentimes, it’s more beneficial to have one or two technicians that are fully dedicated to your account, as opposed to a revolving door of technicians.
- Response Time: How quickly are service calls responded to and what’s the average length of time it takes to resolve issues? Is there a trend? Have things gotten worse or better over time?
- Professional Recommendations: Are you receiving any proactive equipment and/or service recommendations? If so, are you receiving a variety of mid-range and long-term options?
- Financial Analyses: Has your contractor ever completed a full financial analysis on your HVAC system? If not, is there one planned or is there a logical reason behind not performing one?
Related Content: Preventive maintenance case studies from real companies
Have More Questions About Preventive Maintenance?
At BMI Mechanical, we have decades of combined experience providing preventive maintenance for companies all across California. Our technicians and associates know what it takes to create, customize, and implement a service contract that provides all the intended benefits of preventive maintenance. If you need help understanding the ins and outs of your service contract, send us a message today or check out our additional resources.