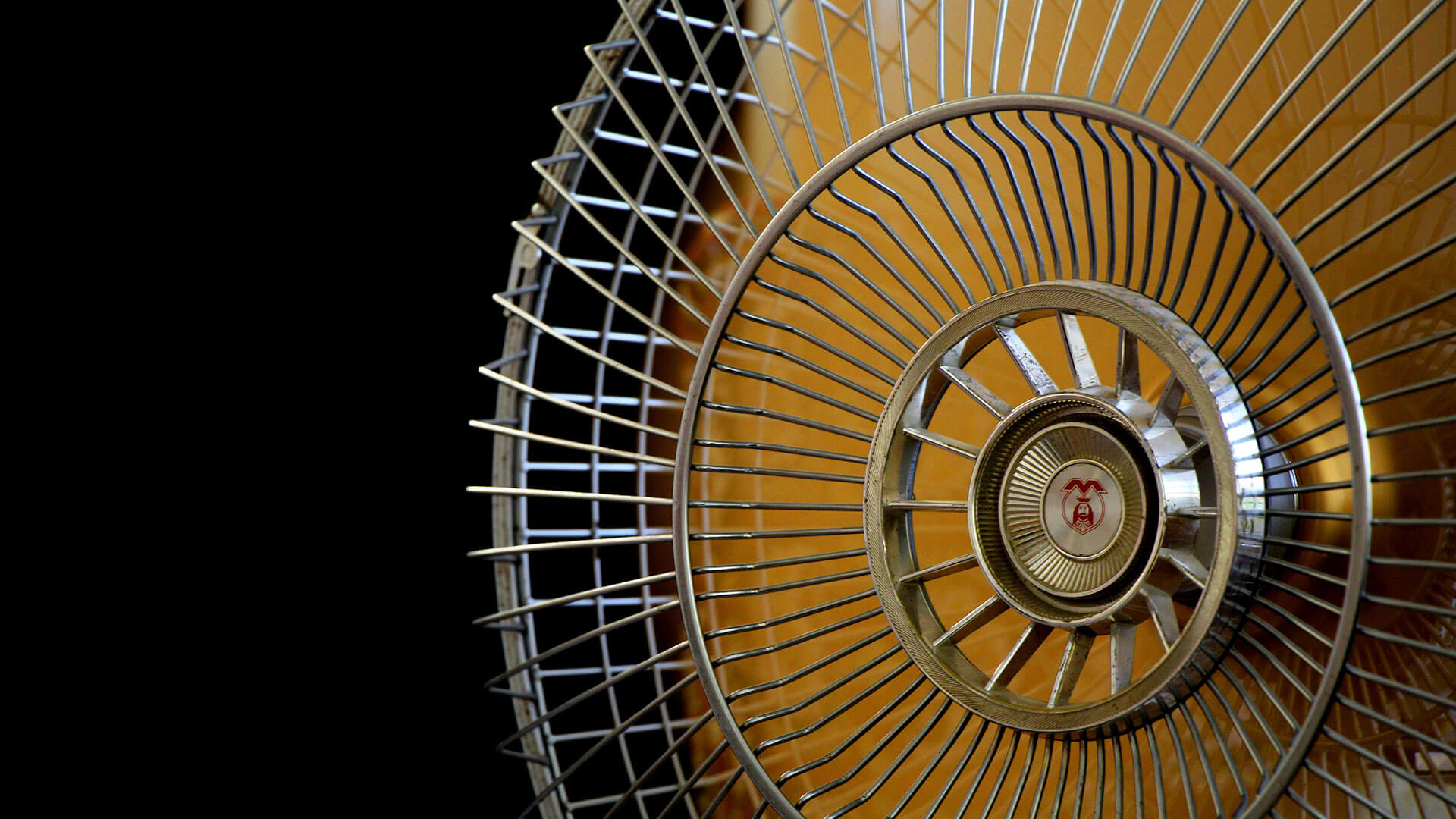
5 Common Summer HVAC Issues
When those hotter months roll around, you’ll likely be running your AC equipment on doubletime. This means that your equipment will be placed under more stress than it’s used to, increasing the risk of unexpected breakdowns in the process.
But where exactly do these issues come from, and what can you do to avoid them? Let’s take a few moments to discuss some of the top reasons HVAC equipment fails in summer and provide you with some simple summer HVAC tips along the way.
5 Common Summer HVAC Issues
Dirty Air Filters
What does it cause?
- refrigerant flooding
- inadequate air flow
- restricted evaporator coil
- not properly cleaned
What’s the result?
- it consumes excess energy
- it can cause the compressor, bearing, or evaporator motor to fail
Dirty Motors
What does it cause?
- windings overheat
What’s the result?
- it can cause the motor component to fail
- consumes excess energy
Refrigerant Leaks
What does it cause?
- lack of lubrication
- improper system charge
What’s the result?
- it can cause the compressor to fail
- consumes excess energy
- the system can freeze up
Plugged Drains
What does it cause?
- water build-up
What’s the result?
- lowers indoor air quality
- promotes the growth of mold and bacteria
- leads to leaks and strong odors
Missing or Loose Panels
What does it cause?
- conditioned air lost
- water infiltration
What’s the result?
- consumes excess energy
- damage to the equipment
- unnecessary rust and corrosion
There are a handful of other common HVAC issues you can expect during hotter months, including faulty drive belts and burnt contact points. However, it’s important to remember that there is a slippery slope — one issue can lead to multiple issues.
This being said, whether it’s one of these issues or multiple issues at the same time, you could find yourself with an HVAC system that doesn’t work at all. If you operate in a sensitive environment that requires a particular temperature, this could result in a complete production halt and end up being way more expensive than it should be.
Keep Reading: When should you repair equipment and when should you replace equipment?
How to avoid summer HVAC issues
The best possible way to avoid summer HVAC issues is with a preventative maintenance solution from a licensed HVAC contractor. Even if you have a barebones maintenance solution, your contractor will still be able to educate you or even warn you about potential problems. This will give you the opportunity to fix issues before they can cause a breakdown, which can definitely end up saving you money in the long run.
In fact, research has shown that for every $1 in deferred maintenance you can expect to spend $4 in future repairs. Not only that, but deferred maintenance can result in increased energy consumption, too. Even something as simple as dirty coils and filters can result in a 30% increase in energy use (via ASHRAE).
Keep Reading: Learn more about how to properly prepare your HVAC for summer
Other unforeseen expenses associated with summer HVAC issues can include a decrease in productivity. With an HVAC system that’s improperly working (or not working at all), employees won’t be as comfortable, and you can expect to see a dip in effectiveness and productivity.
HVAC issues that lead to inadequate ventilation and poorer indoor air quality can also lead to a sudden increase in paid sick leave. According to the National Energy Management Institute, this particular issue can account for 1.5%-6% of annual payroll expenses.
Keep Reading: Learn more about how needlepoint bipolar ionization can improve indoor air quality
Need help preparing your HVAC for summer?
Check out our Spring HVAC Maintenance Checklist and then give BMI a call. We have decades of experience helping businesses keep their HVAC systems working, energy and repair costs low, and indoor air quality high. We’d love to help you, too.
Give us a call or fill out our online form to learn more about our preventative maintenance solutions.